- A+
▲第一作者:牛丛丛 李汉生
通讯作者:夏铭 李德宝
通讯单位:中科院山西煤化所煤转化国家重点实验室
论文DOI:10.1002/aic.17226
钴基费托合成产物以重质烃为主,并且会在催化剂孔道内填充,反应物分子在重质烃产物中较低的扩散系数导致大颗粒催化剂孔道内部存在严重的传质阻力,这不仅大大降低了催化剂的使用效率,还影响了产物选择性。构建多级孔结构催化剂是改善粒内扩散限制、提高催化剂利用效率的重要途径之一。本研究采用实验和模拟相结合的手段定量考察了调变孔结构参数对具有介孔-大孔结构费托合成催化剂大颗粒内的传质过程和反应性能的影响规律。
实验方面:在溶胶凝胶过程中引入相分离制备了一系列具有相同介孔孔径(8 nm),不同大孔孔径(0~6000 nm)的钴基催化剂。评价实验结果显示引入大孔以及增加大孔孔径能够显著提高大颗粒催化剂(10~20目)的反应有效因子,并改善产物选择性。
数值模拟方面:结合多级孔颗粒的孔道结构特点,将大孔孔道内液蜡填充度引入传统颗粒模型,发展了多级孔结构催化剂颗粒的一维稳态传递-反应模型。该模型应用于上述多级孔实验催化剂(10~20目),计算推测蜡填充度随孔结构参数的变化是传质强化的主要原因。将该模型应用于多级孔催化剂2 mm工业颗粒,定量揭示了不同蜡填充度和反应温度、压力条件下孔结构参数影响传质过程和表观反应性能的作用机制。计算结果发现,蜡填充度是影响传质速率的重要因素,在不同的反应条件下通过优化大孔孔径和孔隙率,可达到反应速率和扩散速率的最优匹配,获得最高的C5+时空收率。
费托合成是目前煤、天然气、生物质等含碳资源清洁优化利用的重要途径,该反应对于降低石油依赖度,满足人类日益增长的能源需求具有十分重要的意义。钴基费托合成通常采用固定床技术,固定床工业反应器须装填毫米级(1~3 mm)的催化剂颗粒来保证适宜的床层压力降。然而,研究表明催化剂大颗粒内的传质阻力显著降低了表观反应活性和目标产物的选择性。因此,针对钴基费托合成普遍应用的固定床技术,如何平衡单颗粒催化剂内的扩散距离以及床层尺度上的压力降仍是亟待解决的问题。
本课题组前期制备了大孔孔径为1074 nm的介孔-大孔Co/SiO2催化剂用于费托合成反应,证明了引入传质大孔对传质强化的促进作用。但上述研究未能解释多级孔结构的传质强化机制,实现多级孔结构催化剂的优化设计,仍需要定量分析多级孔结构参数对大颗粒催化剂内的传质性能和表观反应性能的详细影响规律。
(1) 采用溶胶凝胶法制备了一系列具有不同大孔孔径相同介孔孔径的多级孔结构催化剂,定量考察了引入大孔和调变大孔孔径对费托合成大颗粒催化剂表观反应性能的影响规律。
(2) 结合多级孔颗粒的孔道结构特点,将大孔孔道内液蜡填充度引入传统颗粒模型,发展了多级孔催化剂颗粒的一维稳态传递-反应模型,计算得到蜡填充度随孔结构参数的变化是影响传质的重要因素。
(3) 将多级孔颗粒模型应用于多级孔催化剂2 mm工业颗粒,定量揭示了不同填充度水平和反应温度、压力条件下孔结构参数对传质强化和表观反应性能的影响规律。
介孔-大孔SiO2载体中相互连通的大孔结构来自于溶胶凝胶过程的相分离,而介孔来自于氨水的刻蚀。通过精确控制溶胶凝胶过程中相分离和溶胶凝胶的速率,可以得到一系列不同大孔孔径的独巨石SiO2载体。图1扫描电镜(SEM)结果显示,载体S0不具有大孔结构。只有当PEG加入量适宜时,相分离和凝胶化的速率相匹配,制备的载体材料才呈现双连续的贯通大孔结构。除了S0,其余7个载体材料都有类似蜂窝状的大孔结构。随着PEG的用量增加,大孔孔径越来越小,即从S6000到S50介孔-大孔SiO2载体中的大孔孔径依次变小。
▲图1 SEM images of the prepared supports.
压汞实验(图2a)和SEM照片得到的结果一致,即从S50到S6000,制备的SiO2载体大孔孔径由50 nm增加到6000 nm。上述载体及其催化剂的织构性质通过N2物理吸附表征,如图3所示,载体及其对应的催化剂都具有比较接近的介孔孔径分布。S50及其对应的催化剂介孔孔径分布范围很广,这是因为除了氨水刻蚀得到的介孔以外,相分离得到的大孔尺寸为50 nm,也在BET结果中得以体现。综合SEM、压汞测试以及氮气吸脱附结果,我们证实S0及其对应催化剂具有单一介孔结构(约8 nm),其余样品均具有介孔-大孔结构。XRD谱图结果(图2b)表明所有催化剂均为尖晶石相Co3O4,且通过谢乐公式计算的晶粒尺寸都非常接近,这是因为载体的介孔孔径以及比表面积非常接近。其中催化剂Co/S50和Co/S150的晶粒尺寸相比其余催化剂略大,这是因为其大孔孔径较小,影响了活性组分在孔道内的成核长大过程,而其余介孔-大孔载体的大孔较大,不会影响催化剂的晶粒尺寸。图2c表明所有催化剂具有类似的还原行为,活性组分和载体相互作用形成的难还原钴硅物种的还原峰很小,说明活性组分和载体相互作用较弱。其中Co/S50和Co/S150的第二个还原峰略大,这主要是由于其相对较大的晶粒尺寸。 ▲图2(a) Macropore size distribution of the prepared supports from mercury intrusion porosimetry and (b-c) XRD patterns and H2-TPR curves of the prepared catalysts. ▲图3 Pore size distribution of supports (a) and corresponding catalysts (b) determined by N2 adsorption/desorption isotherms. 稳态条件下不同大孔孔径的多级孔催化剂大颗粒(10~20目)评价实验结果(图4)显示,随着大孔尺寸的增加,催化剂的CO转化率整体呈现先增加后稳定的变化规律。其中Co/S50和Co/S150的CO转化率偏离规律曲线,可能是因为其具有较大的晶粒尺寸,活性组分分散度较低,暴露的活性位点数较少。总体来讲,随着大孔孔径的增加,费托合成表观活性不断提高,大孔孔径大于2100 nm之后,继续增加大孔孔径活性增加幅度较小,表明此时内扩散阻力的影响已经接近完全消除。产物选择性随着大孔孔径的变化规律也得到了相同的结论,随着大孔孔径的增加,颗粒内H2/CO比逐渐降低,并接近气相主体的H2/CO比,产物逐渐重质化,当大孔孔径大于2100 nm之后,产物选择性几乎恒定不变。因此,大孔孔径为6000 nm时的表观反应性能可作为该催化剂的本征反应性能。 ▲图4 Effect of macropore diameter on (a) CO conversion and (b) CH4 and C5+ selectivities 考虑到大孔SiO2载体中介孔是通过氨水刻蚀形成的,其主要存在于大孔孔壁上,且深入距离较短,因此,介孔内的扩散阻力可以忽略不计,只考虑大孔中的扩散阻力。该介孔-大孔的多级孔结构可以用图5所示的简图来表示。基于上述假设,本研究结合多级孔颗粒的孔道结构特点,将大孔孔道内蜡填充度引入传统颗粒传递-反应模型,发展了多级孔催化剂的一维稳态颗粒模型。 ▲图5 Illustrations of the meso-macropore networks. 对实验催化剂颗粒(10~20目)的模拟结果表明,传质强化的原因主要是大孔降低了蜡填充度,另外,Knudsen扩散系数的增大和大孔孔隙率的增加也是促进传质强化的原因。但是,计算结果发现大孔尺寸大于200 nm以后,Knudsen扩散对于传质强化的贡献可忽略。 ▲表1 Calculation results of filling degree within the catalysts in experiment based on the pellet modela 2 mm工业催化剂颗粒的模拟结果(图6)表明,蜡在孔道内的填充度是影响传质大小的重要因素;且存在最优的孔隙率值,使得扩散速率和单位体积的反应速率实现最优匹配,以获得最高的C5+时空收率。只有在不完全填充,且催化剂颗粒处于扩散控制时,提高大孔孔径才会明显改善传质和表观反应性能;当大孔孔径大于200 nm时,Knudsen扩散系数已经远大于气相分子扩散系数,此时气相分子扩散成为影响传质的控制因素,因此,200 nm可作为此反应条件下的最优大孔孔径。在温度为200~240℃,压力为2.0 MPa,原料H2/CO比为2.0,液蜡填充度F为0.6的条件下,介孔和大孔孔径分别为8 nm和200 nm的多级孔催化剂颗粒,孔隙率在0.40~0.58范围内,C5+时空收率为0.724~1.354 g/mLcat·h,比相同条件下具有单一介孔的催化剂提高了22~206%。 ▲图6 of the meso-macropore catalyst pellets with different macropore diameter and filling degree at the temperature of 473, 493 and 513 K. The pressure was 2.0 MPa, H2/CO was 2.0. 不同反应压力条件下的多级孔催化剂的优化计算结果表明,提高反应压力有利于2 mm催化剂C5+时空收率的提高;这可以归因于反应压力提高对反应活性和传质速率两个方面的促进作用。反应压力的这种促进作用在相对低压范围内(1.0~3.0 MPa)更加显著,这要归因于费托合成的本征反应特性,即高CO分压对反应速率的抑制作用。对于介孔和大孔尺寸分别为8和200 nm的多级孔催化剂颗粒,在反应温度为240℃,原料H2/CO为2.0,液蜡填充度为0.6条件下,反应压力从1.0 MPa提高至4.0 MPa,最优STYC5+从1.006 g/mLcat·h提高至1.621 g/mLcat·h,对应的最优孔隙率在0.56~0.61范围内。 ▲图7 of the meso-macropores catalyst pellets with different macropore diameter at the total pressure of 1.0, 2.0, 3.0 and 4.0 MPa. The reaction temperature was 513 K, H2/CO was 2.0, filling degree was 0.6. 本研究通过在溶胶凝胶过程中控制相分离速率,精确调控了SiO2载体的大孔孔径,并获得了一系列相同介孔孔径(~8 nm)、不同大孔孔径(50~6000 nm)的Co/SiO2催化剂。评价实验结果表明引入大孔和增加大孔孔径能够有效促进传质、改善催化剂的表观反应性能。进一步发展了考虑蜡填充度、多级孔结构参数的颗粒模型,计算推测实验过程中增加大孔孔径促进传质强化的主要原因是蜡填充度的降低和大孔孔隙率的增加。2 mm多级孔工业催化剂颗粒模拟结果表明,蜡填充度是影响传质的重要因素,通过优化大孔孔径和孔隙率可以获得最优的C5+时空收率。温度越高,多级孔强化传质的效果越显著;在低压范围内(1.0~3.0 MPa)提高反应压力可显著改善催化剂的表观反应性能。本研究结论为多级孔工业催化剂颗粒的优化设计与性能调控提供了理论基础,本研究方法可拓展至其它气-液-固三相催化反应体系的多级孔催化剂颗粒的工程设计。
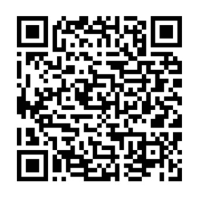
目前评论: